Advanced Techniques in Modern Tank Welding Inspection
The Necessary Function of Tank Welding Examination in Ensuring Structural Honesty and Security Compliance in Industrial Applications
In the realm of commercial applications, container welding inspection emerges as a crucial element in guarding structural stability and guaranteeing conformity with safety and security guidelines. Utilizing a combination of strategies such as visual evaluations and progressed testing methods, these evaluations offer to recognize and alleviate possible imperfections before they rise right into substantial dangers.
Value of Storage Tank Welding Inspection
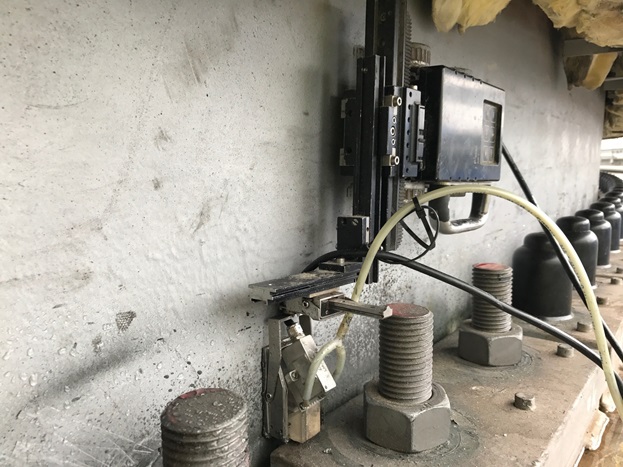
Making sure conformity with market requirements and policies is another substantial facet of container welding evaluation. Regulatory bodies mandate strict standards for the building and maintenance of storage space tanks, and detailed examinations assist companies follow these demands. Non-compliance can lead to serious charges, including fines and shutdowns, better stressing the need for extensive evaluation protocols.
Additionally, tank welding examination plays a vital function in keeping functional efficiency. In recap, the significance of container welding evaluation exists in its capacity to safeguard public wellness, safeguard the setting, and guarantee compliance with regulative frameworks.
Secret Examination Techniques
Efficient container welding evaluation relies upon a variety of essential strategies that make certain comprehensive assessment of weld top quality and structural stability. Among the most common methods are aesthetic examination, ultrasonic screening, radiographic testing, and magnetic particle testing - Tank Welding Inspection. Each technique supplies unique advantages in examining various elements of the weld
Aesthetic inspection acts as the very first line of protection, permitting inspectors to identify surface problems, irregularities, or inconsistencies in the weld grain. Ultrasonic screening uses high-frequency acoustic waves to spot interior problems, such as splits or voids, supplying an extensive assessment of weld honesty. This technique is especially efficient in finding concerns that might not show up externally.
Radiographic screening uses X-rays or gamma rays to produce pictures of the welds, exposing internal suspensions and giving an irreversible document for future referral. This strategy is extremely efficient for important applications where the threat of failing need to be lessened.
Finally, magnetic bit testing is employed to identify surface and near-surface flaws in ferromagnetic materials. By using electromagnetic fields and fine iron particles, inspectors can pinpoint interruptions that may jeopardize the architectural stability of the container. Together, these techniques create a durable structure for guaranteeing premium welds in industrial applications.
Conformity With Safety Standards
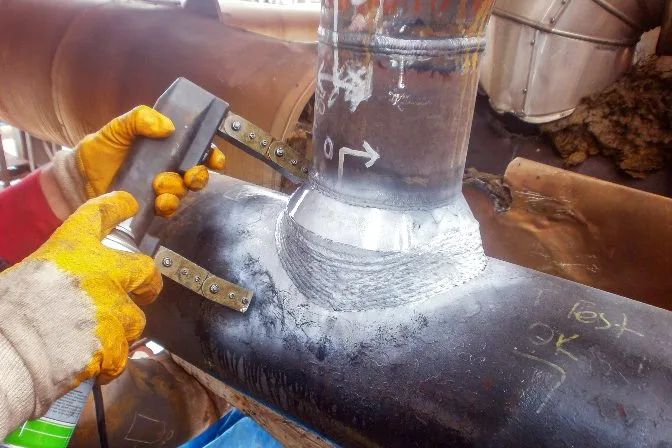
Normal assessments play a crucial role in ensuring conformity by identifying possible failures or deviations from recommended standards. Assessors are educated to click now examine weld top quality, verify material requirements, and evaluate the total structural honesty of tanks. Their expertise is crucial in making certain that welding procedures fulfill the needed safety and security requirements.
Furthermore, conformity with safety standards not only secures workers but also safeguards the environment from prospective threats such as leakages or tragic failings. Organizations that focus on safety compliance are much better placed to reduce dangers, boost operational effectiveness, and promote a culture of safety and security within their workforce. In recap, keeping rigorous compliance with safety and security criteria is important for the successful operation of tank welding tasks in commercial settings.
Benefits of Routine Assessments
Normal inspections are essential to keeping the structural integrity and safety and security of bonded containers. These examinations provide a systematic method to determining prospective issues or weak points in the welds, guaranteeing that any problems are attended to prior to they rise right into substantial failings. By performing normal assessments, companies can spot deterioration, tiredness, and other types of degeneration that may jeopardize storage tank performance.
Furthermore, consistent assessments add to conformity with sector guidelines and requirements. Sticking to these standards not just alleviates lawful threats but also improves the organization's credibility for security and reliability. Regular examinations promote a proactive safety society, urging employees to recognize and focus on the value of devices integrity.

Study and Real-World Applications
Study and real-world applications highlight the concrete influence of reliable container welding assessment practices. One remarkable instance is a large petrochemical center that dealt with substantial functional disturbances as a result my website of leakages in tank. Complying with the execution of extensive welding inspection methods, including aesthetic and ultrasonic testing, the center identified essential imperfections in weld joints that might have brought about disastrous failings. This aggressive technique not just prevented ecological threats however likewise conserved the company millions in prospective cleanup costs and regulatory penalties.
In a similar way, a water therapy plant applied an extensive assessment program for its container welding operations - Tank Welding Inspection. By incorporating non-destructive testing approaches, the plant had the ability to find early signs of corrosion and tiredness in weld joints. This timely treatment expanded the life-span of the tanks and ensured compliance with security policies, hence securing public health
These study emphasize the importance of regular and systematic tank welding evaluations. By prioritizing these practices, markets can mitigate dangers, boost architectural honesty, and make certain conformity with safety and security criteria, inevitably resulting in enhanced functional effectiveness and minimized liabilities.

Verdict
Finally, container welding examination is a vital part of maintaining structural honesty and safety and security in industrial applications. Employing various inspection strategies ensures early detection of prospective flaws, thereby protecting against tragic failings. Adherence to security requirements better boosts operational reliability and conformity with regulative needs. Eventually, regular inspections not just safeguard public health and the setting but additionally add to the longevity and effectiveness of crucial assets, highlighting the vital role of this method in industrial procedures.